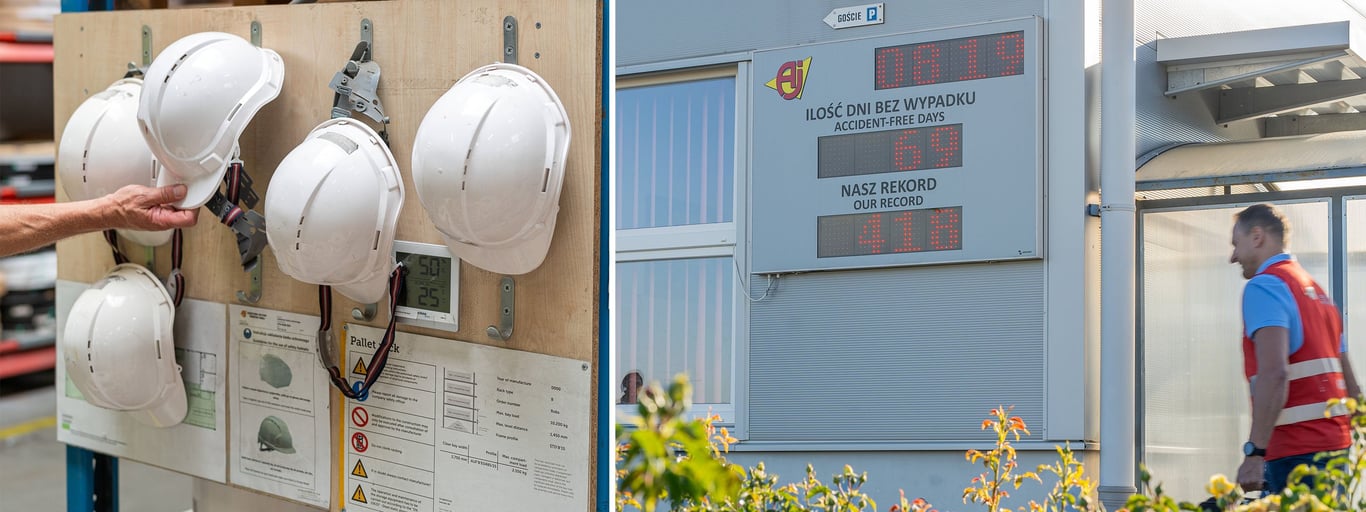
The importance of employee health and safety in manufacturing
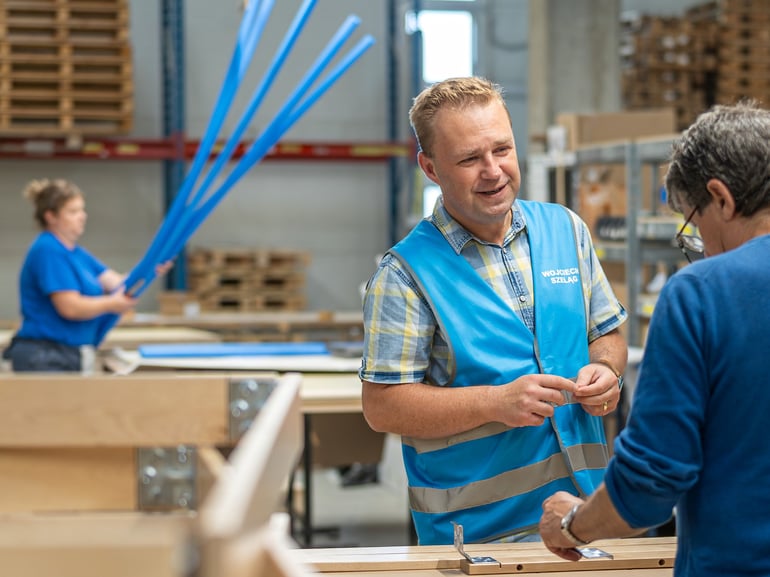
“In mid-2021, we first reached a record of 365 accident-free days, then we increased it to our current record. My greatest success in my years at AJ Products has been achieving 418 days without a single accident,” he says.
So what's the recipe for a workplace where accidents are so rare? Wojciech believes that a good safety approach starts at the very beginning. Before a new employee enters the production hall, a detailed protocol is followed.
“During the initial training for new hires, we start by familiarising them with safe lifting techniques. The staff receive training on how to lift correctly and how much they can lift depending on gender and stature. They also learn correct ergonomic work positions,” Wojciech explains.
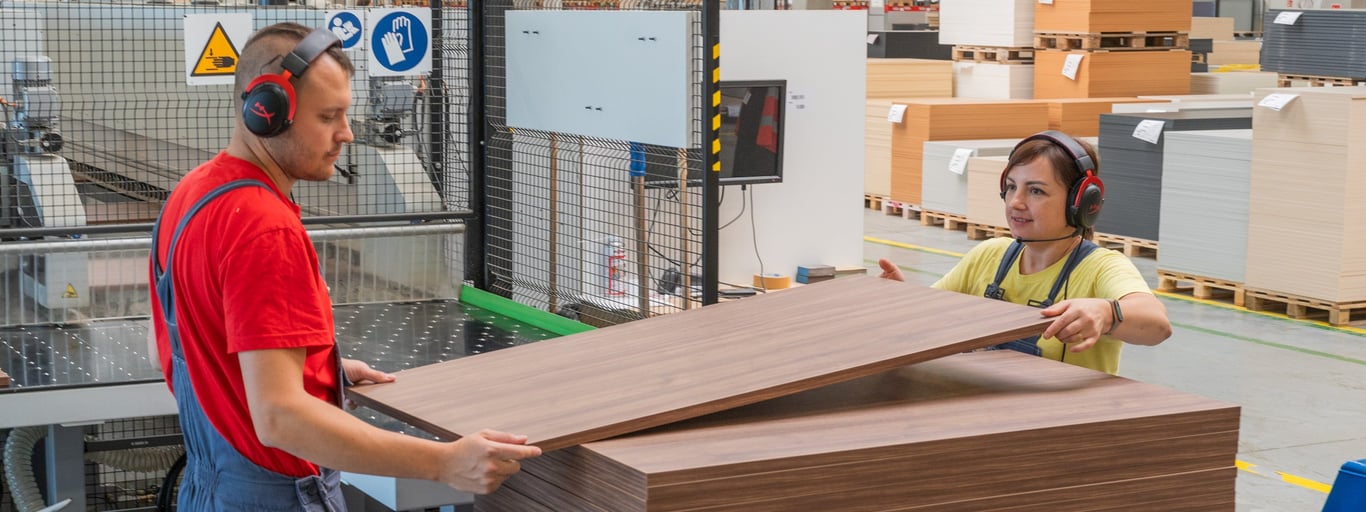
Careful risk management and safety development with BBS
To manage work-related risks, all potential risks and hazards are recorded in a safety model and then discussed during weekly meetings with the factory managers.
“Then we develop measures to prevent such situations or similar issues from occurring,” explains Wojciech.
He also notes that the factory's safety improved significantly when they introduced BBS in 2019. BBS stands for Behaviour-Based Safety. Among other things, this involves representatives from the production department and from management discussing improvement measures together with the personnel working on the factory floor.
Read more about AJ Furniture Factory's leadership model
Wioleta Kowalik is the factory manager at AJFF and sees safety and ergonomics as an incredibly important piece of the puzzle in the factory's development. She and the management team continually review technical changes they can make to streamline processes and minimise the risk of injury on the production floor. For instance, they are considering investing in a loading robot in 2024 that could eliminate the lifting of larger assembled furniture.
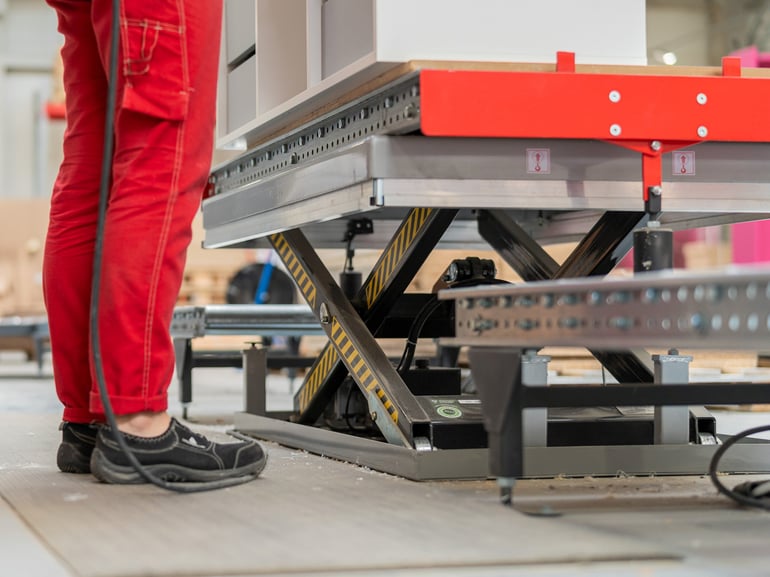
However, smaller changes can also make a big difference. Working in a factory means a lot of standing work, which is demanding on the body and can cause strain injuries. Therefore, the plan is to provide more ergonomic aids throughout the factory.
“We are planning to equip all workstations where employees carry out standing tasks with supportive anti-fatigue mats. We’ll also provide platforms for employees whose workbench cannot be lowered to suit their height because two people of different heights may need to work in pairs at the same workstation,” says Wioleta.
A healthy and safe environment from floor to ceiling
Wojciech explains that management has decided that no financial resources should be spared when it comes to improving working conditions and purchasing high-quality protective equipment. The staff has full access to all the necessary PPE they may need for their specific tasks. If anyone needs new steel-capped boots, gloves or ear protection, it will either be available in the production manager's office or can be ordered right away. Scattered around the premises are dispensers with small earplugs in case they are quickly needed, and in departments where a safety helmet is required, they are readily available at the entrance.
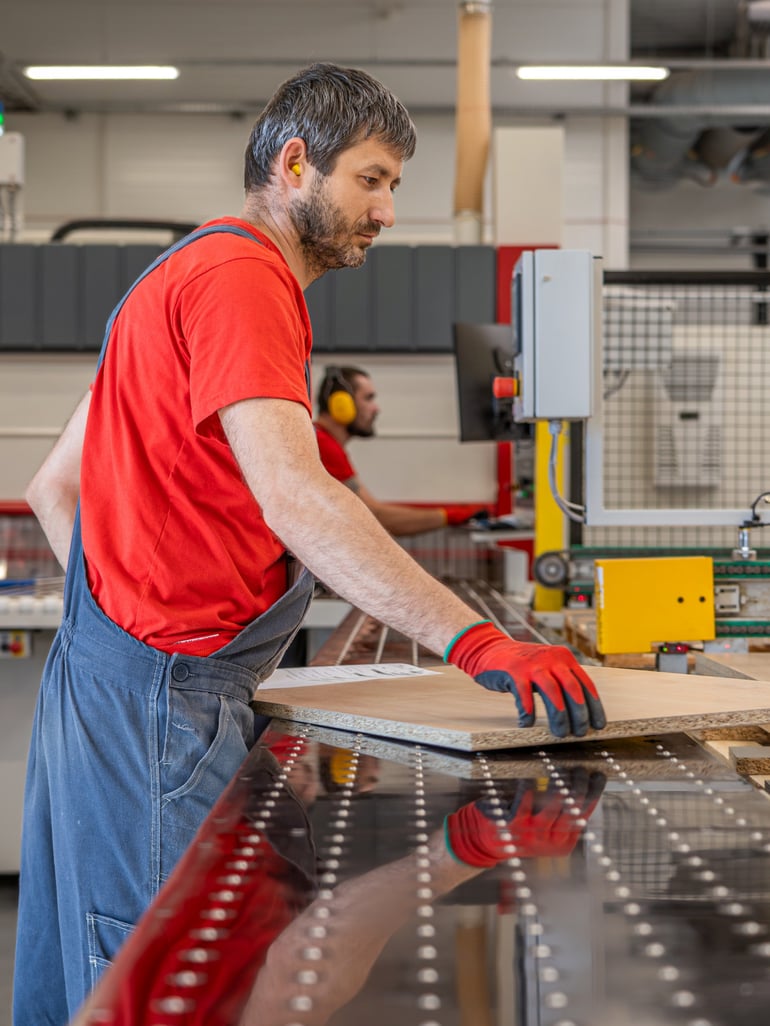
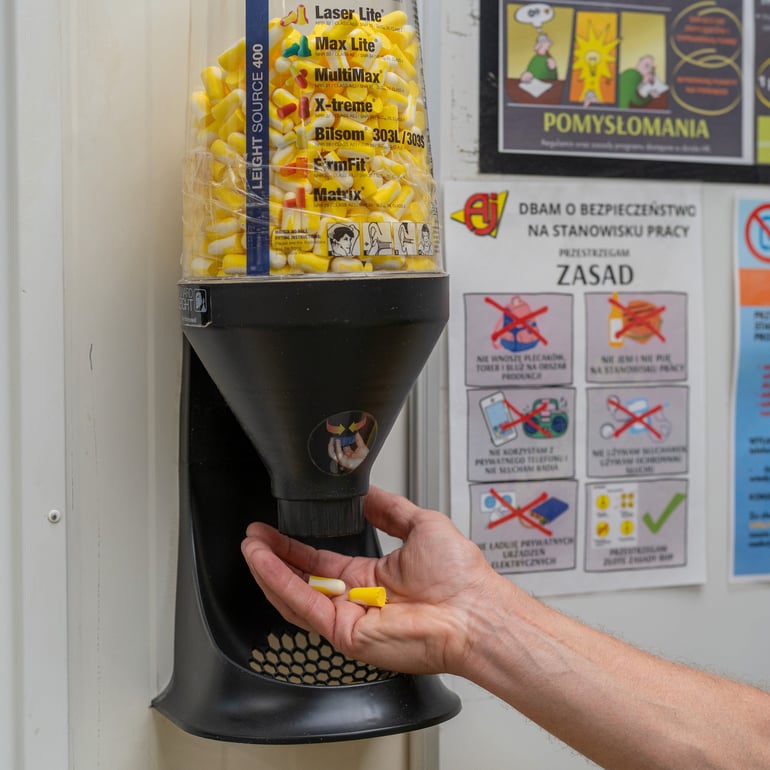
In the paint department, the number of accident-free days is currently over 2000. Since only water-based paint is used, it does not emit a strong odour and is not as hazardous to health or the environment as oil-based paint. Wood chips and particles, which naturally occur when working with wood, are filtered out of the air through an effective ventilation system in the ceiling that is present throughout all parts of the factory.
On the floor in the production halls, bright green lines run straight through the large spaces. Combined with traffic mirrors and safety barriers, these lines make it clear where the staff should walk to keep a safe distance from forklift traffic. Yellow lines indicate instead where materials, pallets and goods should be placed. In an environment that could easily become messy and dangerous, there is a clear balance where everything, and everyone, has a place.
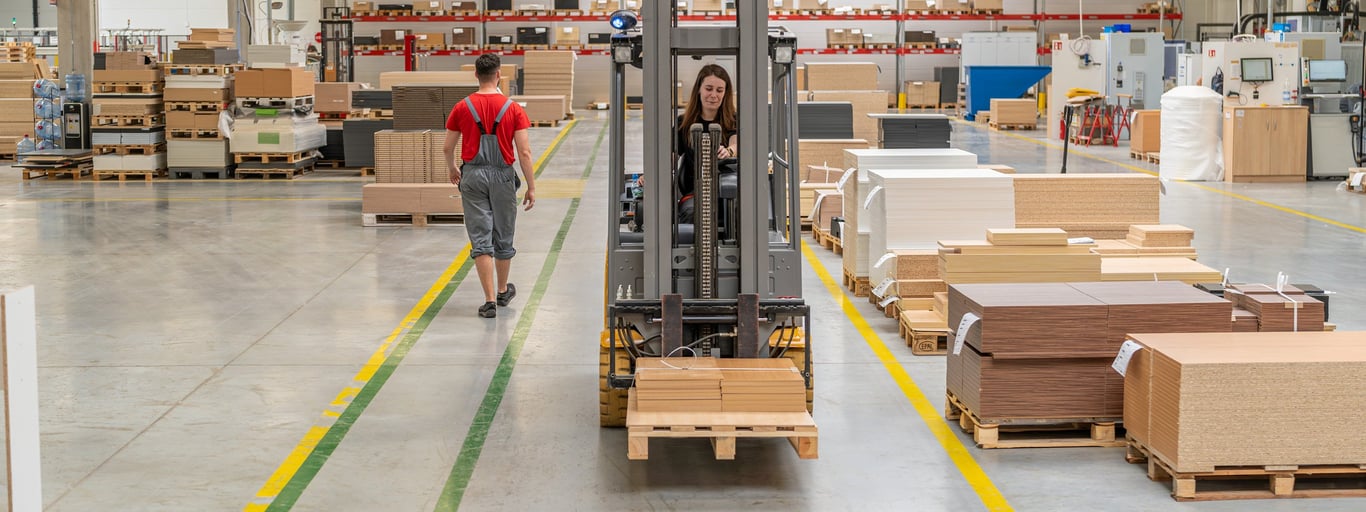
Get the latest product launches and offers sent direct to your inbox
Do you want to receive exclusive offers, information about new products and inspiration on how you can improve your workplace? Sign up for our free newsletter and be the first to receive our best offers.*By clicking subscribe, I confirm that I have read the privacy policy.